High efficiency and energy saving:
①High power density: The power density of sand mill is 300kW/m³, and the power density of ball mill and tower mill is 20-30kW/m³;
②Large specific surface area of medium: Compared with the grinding medium of ball mill with φ50mm, the surface area per unit volume of φ3-5mm grinding medium of sand mill is increased by 20 times;
③Selective grinding: The grinding characteristics of bead mill "large grinding large, small grinding small" to realize high efficiency grinding.
Internal classification of open circuit grinding:
①Open circuit grinding, closed circuit effect, no matching classification equipment is required, the process is simple and easy to operate;
②Avoid over-grinding and under-grinding caused by low classification efficiency, and the product has a narrow particle distribution, which is conducive to improving flotation indicators.
Save on infrastructure investment:
①Small footprint, with the same processing capacity specifications, the cylinder volume is less than 20% of the ball mill;
②Low requirements for plant height. The equipment is horizontal, and the highest point of the equipment does not exceed 2.7m.
Safety and environmental protection:
① The equipment uses 2-4mm grinding balls for grinding, the medium volume is small, and the cylinder is lined with wear-resistant materials;
② The equipment adopts sealed connection, there is no powder pollution during equipment operation, and the cylinder is basically noiseless during equipment operation.
Reliable and convenient:
① The equipment is easy to operate, operates smoothly, and is convenient for the automated management of mines;
② The daily ball consumption of nano-ceramic balls is less than 1/10 of that of steel balls, and the labor intensity is low.
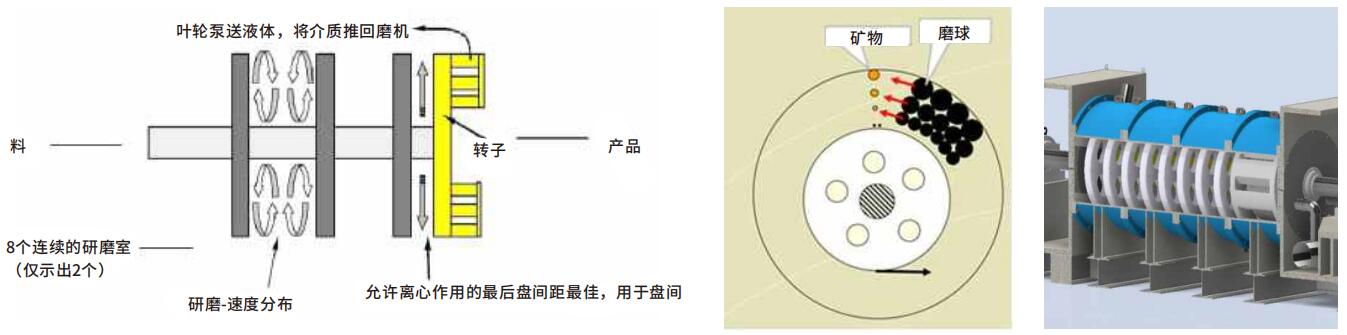
(1) After the slag is separated, the slurry is stably fed into the mill through a hose pump. The stirring disc in the cylinder rotates at high speed under the drive of the main shaft, so that the grinding medium moves around the axis and rotates on its own axis. The mineral particles are scrubbed by the high-speed moving grinding medium to achieve the grinding process.
(2) There is an independent grinding area between each two discs. Under a certain feeding pressure, the slurry becomes finer as it moves further back, realizing the new process of internal grading and open-circuit grinding.
(3) Under the action of high-speed rotating centrifugal force, the minerals and grinding media are radially distributed from the inner wall of the mill axial cylinder according to the particle size from small to large, realizing the selective grinding of "large grinding large, small grinding small".
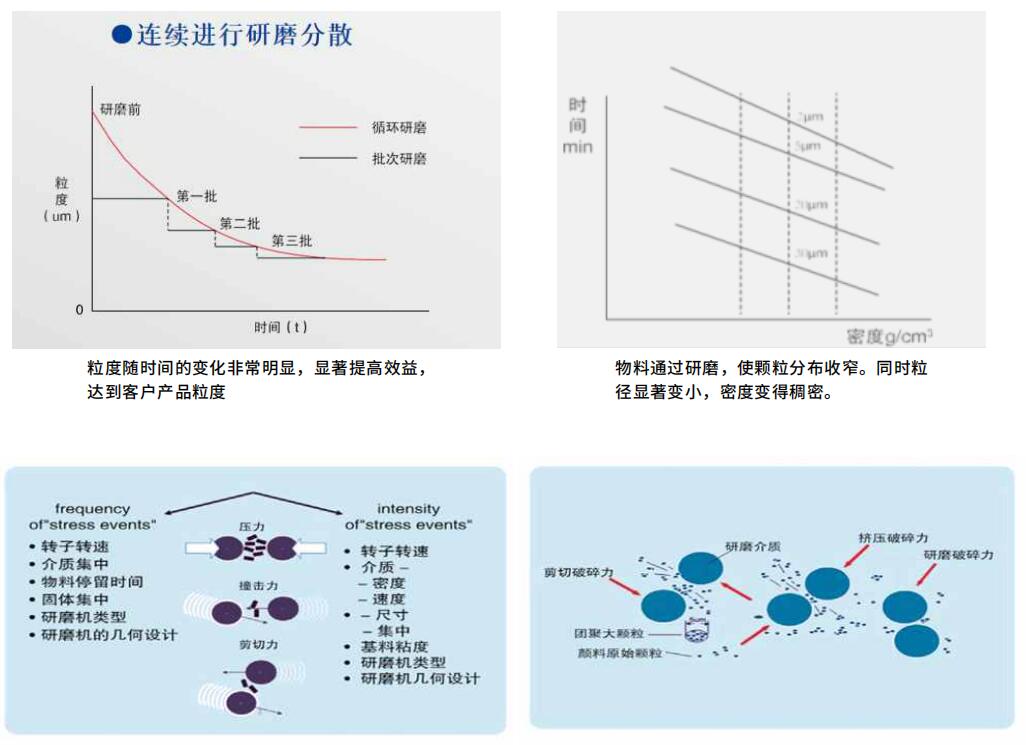