From industrial computers, DCS or PLC modules, industrial configuration software, cabinets, consoles, relays, AC contactors, thermal
relays, air switches, etc. inUnder WinXP English environment, using the actual flow chart drawn by the industrial configuration software, the
crew operation personnel can realize the operation of the unit through various screens displayed on the operation station for operation and
monitoring. Each frame can display the real-time data of the weighing process variable and the status of the running equipment. The data and
status update cycle is once per second.
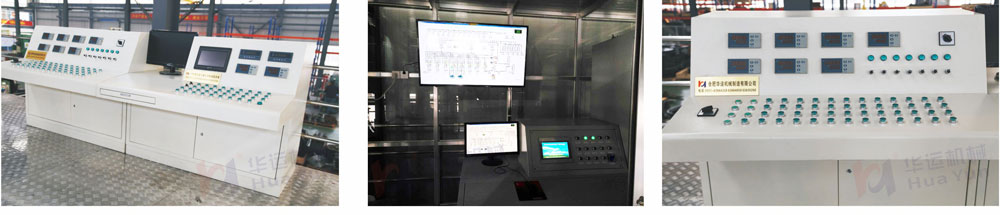
Characteristics:
1.Hardware:
a. The main components of the system are customized or purchased from well-known manufacturers at domestic and abroad, are strictly
used after screening.
b. All module cards are intelligent, using advanced production and manufacturing equipment and advanced detection equipment, with
automatic correction function to ensure the system's control accuracy.
c. The system has a large load capacity: The total number of control tests can be within 20,000 points, fully meeting the requirements.
d. The main controller CPU of the system control station adopts advanced high-performance embedded industrial grade CPU chips
(imported), and is configured in 1:1 redundancy (pair redundancy) to ensure maximum protection.Demonstrated the reliability of the control
station.
2. Software:
a. Adopt advanced and optimized control software that can meet various control requirements.
b. The configuration and control software is easy to learn and use. The display animation shows the workflow and related animations.
The operator can intuitively know the working status of the device. Just use the mouse to easily complete the production.
c. The system communication network adopts standard industrial Ethernet and has good openness. It can be connected to the enterprise
management system through multi-functional stations and corresponding software.
d. The system can be configured online, debug online, and downloaded online, which greatly reducing the number of shutdowns caused
by automatic control of the production system.
e. The parameters can be modified, saved, and recalled to the current work at any time to increase productivity.